Aluminum alloy castings are used in most motorcycle engines and gearboxes as blocks, caps and load-bearing elements. After many years of operation, even with loose screws, in bad weather conditions, they usually require repair. Broken threads, oil caps sealed with tow, uncalibrated holes for centering sleeves, as well as huge tears caused by broken or loose chains – this is an everyday occurrence when working with oldtimers. How to deal with this?
Restore all casting details to factory shape.
Typically, the TIG AC welding method is used for this purpose. It is electric welding using a non-consumable electrode and material added by hand. This method is commonly used when joining aluminum alloys, repairing blocks and covers, and also in aluminum structures. It allows you to make a weld with or without adding material – just melting the native material. It requires a steady hand and experience to obtain an aesthetic weld face and proper penetration, and therefore high strength properties. The selection of the electrode, filler metal and welding parameters is very important. Silicon binder is usually used and is suitable for welding castings. Why?
Castings are usually made of an aluminum-silicon alloy. The percentage of silicon added is indicated by the features on the blocks, covers and bodies. Below we see the LA2A alloy – this is how the later AK9 was once designated, i.e. AlSi9. Such an alloy contains the addition of silicon in an amount ranging from 8 to 11% (by weight).
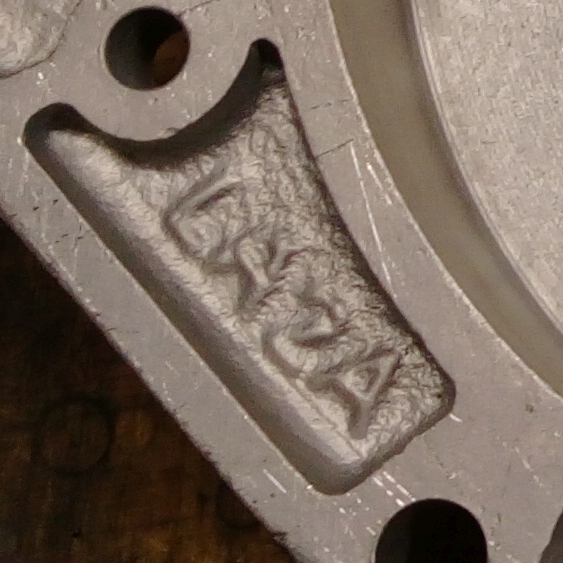
The addition of silicon reduces the thermal expansion of the alloy and therefore increases its thermal stability. Thanks to this, the pistons do not swell and the bearings do not fall out of the seats of the heated body.
The composition of the binder should be as close as possible to the composition of the native material. Otherwise, cracks and other damage may occur.

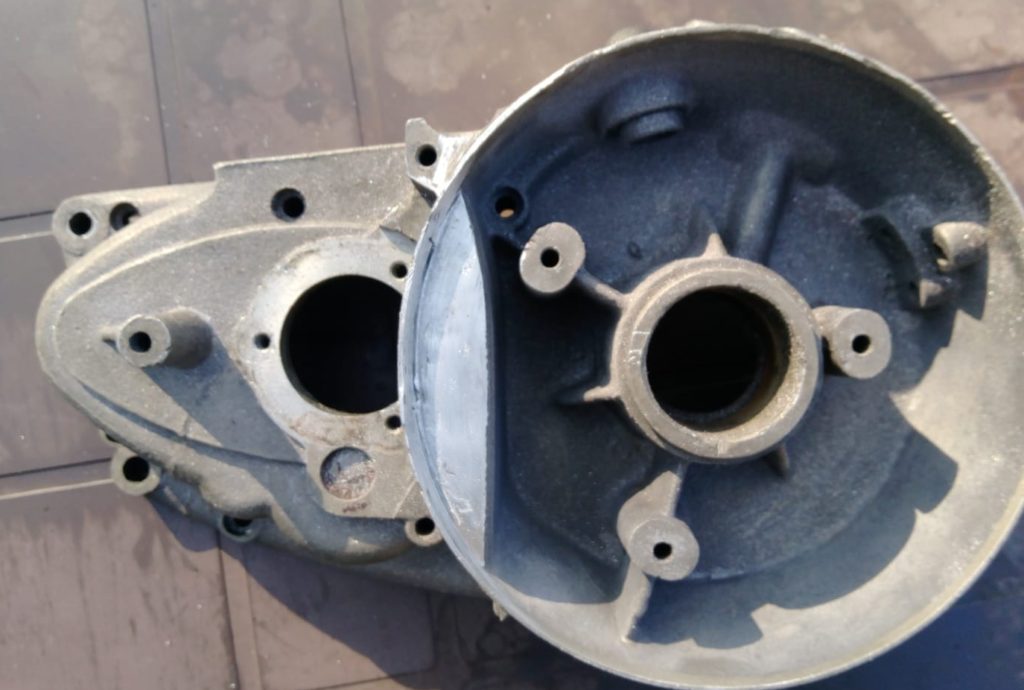
However, proper welding of the element does not guarantee a properly performed repair. All that remains is to process the weld in such a way that it is:
– aesthetic
– close or identical to the original shape of the element
– did not interfere with the elements cooperating with the housing
In some places, in the case of a casting structure poorly developed by the manufacturer, it is worth welding in reinforcement or strengthening the element with just the weld.
The weld processing itself is a great opportunity for a skilled hand, ingenuity in the use of machines and tools, as well as patience in manual work. Below is an example of repairing the thread of the oil drain plug in the S01 engine crankcase. In the original it is an M14x1.5 thread. In the crankcase I found an M16x1.5 thread, very deformed, practically on the verge of breaking. The repair stages presented in the photos are:
– cleaning and welding the old hole
– planning of the plug seal seat
– drilling a hole for the thread
– hole threading M14x1.5

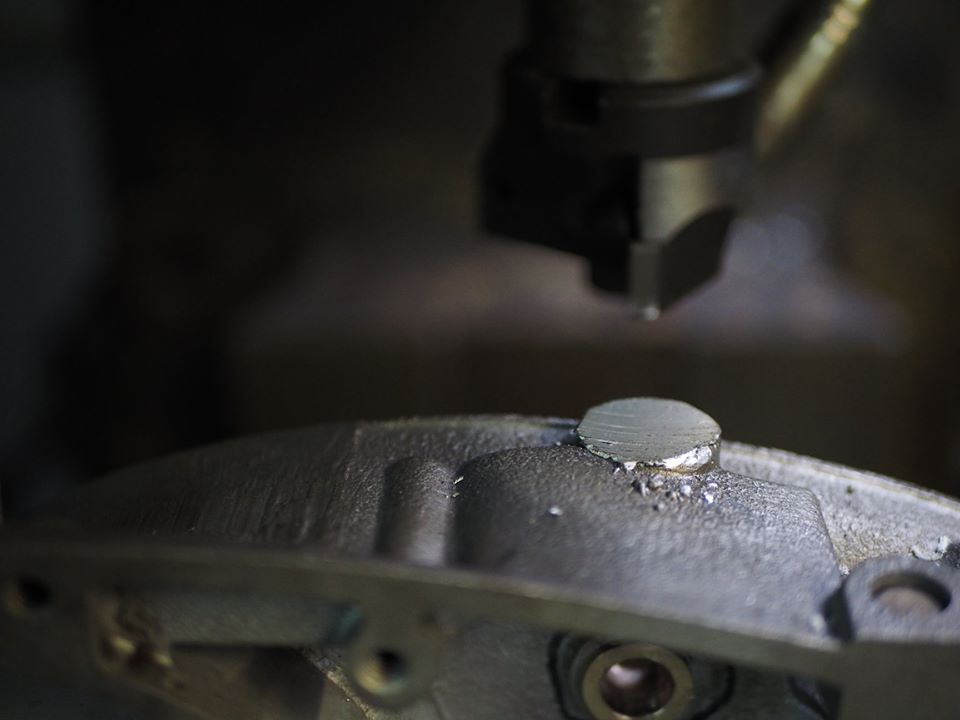
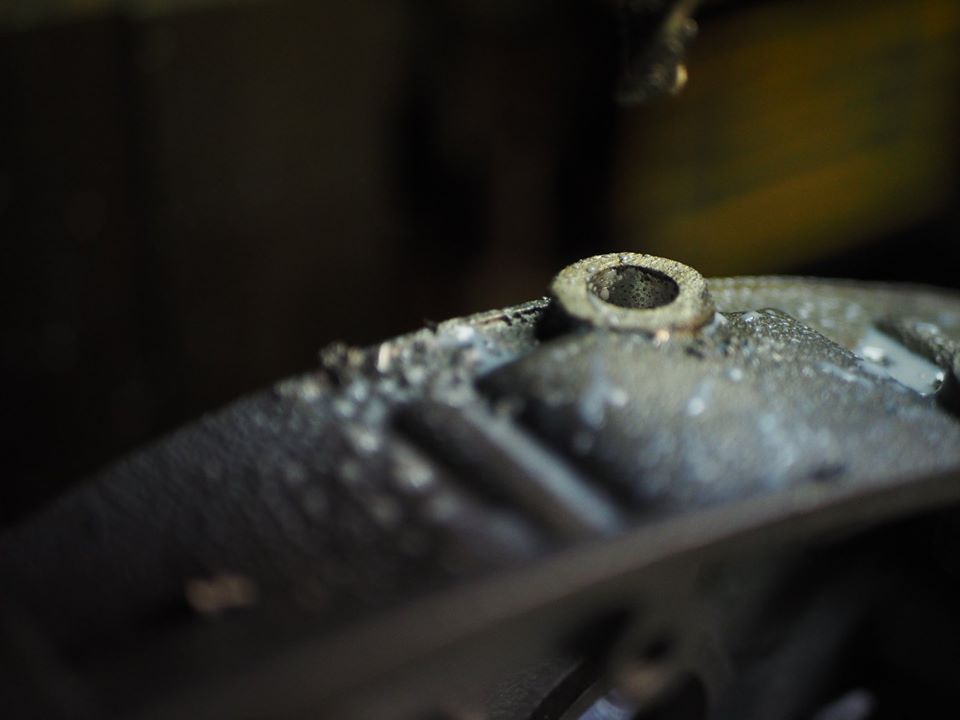
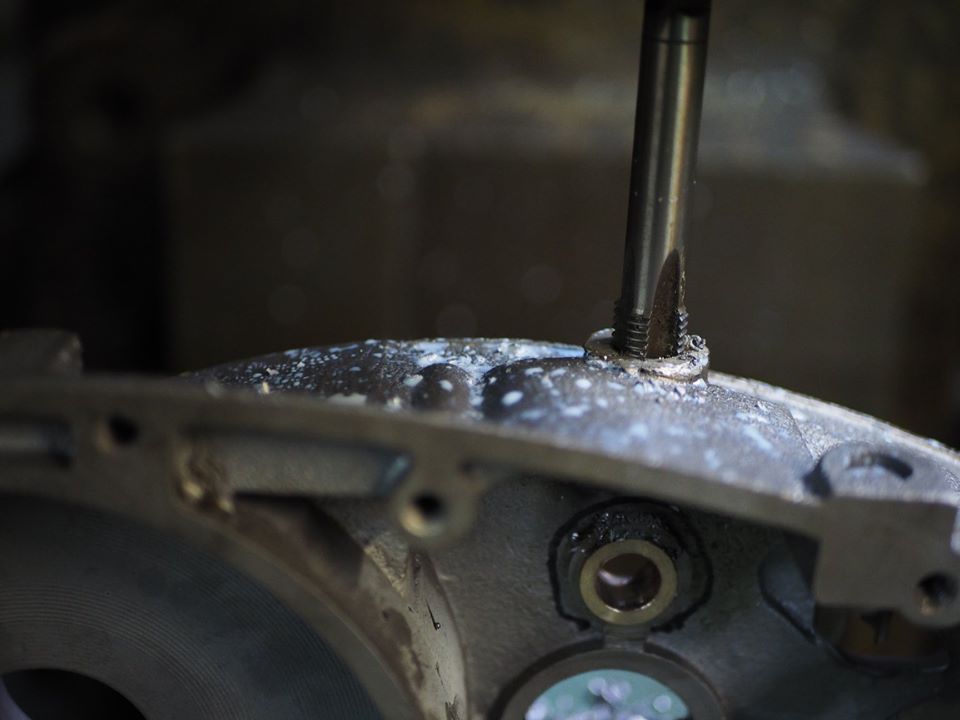
The effect of the repair is visible on the right.
